해부 후 육안 검사 또는 결함 감지를 위해 기공은 매끄러운 표면과 원형 모양을 갖습니다.
원인:
1. 용융 알루미늄의 도입 방향이 불합리하거나 용융 금속의 유속이 너무 빨라 분사가 발생합니다.
2. 공기를 감싸는 와류를 형성하기 위한 배기 덕트 또는 정면 충격벽의 조기 막힘.
3. 충전물이 깨끗하지 않거나 제련 온도가 너무 높기 때문에 용융 금속의 더 많은 가스가 제거되지 않고 응고 중에 침전물을 완전히 배출할 수 없습니다.
4. 이형제는 기체의 양이 많거나 너무 많이 사용되며, 주물에 기체가 연루되어 있어 주물 전에 붓지 않고 기공이 대부분 짙은 회색 표면으로 되어 있다.
5. 고속 스위칭 포인트가 잘못되고 압력이 너무 낮고 흐름이 너무 작습니다.
개선방안(전제: 주입시 비산물질 없음)
1. 깨끗한 충전물을 사용하고 제련 온도를 제어하며 가스 제거 처리를 수행하십시오.
2. 합리적인 공정 매개 변수, 사출 속도, 고속 스위칭 포인트, 에너지 저장 압력, 사출력, 흐름 개방 등을 선택하십시오.
3. 금속 액체 균형을 유도하고 공동을 질서 있게 채우고 가스 배출을 용이하게 합니다. 주자를 향상시키는 것이 필요합니다.
4. 배기 슬롯과 오버플로 슬롯은 충분한 배기 용량을 가져야 하며, 필요한 경우 슬래그 백과 배기 슬롯을 늘리거나 확장합니다.
5. 공기량이 적은 이형제를 선정하여 공기량을 조절한다.
수축
1. 해부학적 또는 결함 감지, 공동의 모양이 불규칙하고 매끄럽지 않고 표면이 어둡습니다.
2. 크고 집중된 수축 기공은 수축 기공으로 작고 흩어져 있습니다.
원인:
1. 주물의 응고 과정에서 수축으로 인해 액체 금속을 보상할 수 없어 공동이 생깁니다.
2. 주입 온도가 너무 높고 금형 온도 구배 분포가 불합리합니다.
3. 분사율이 낮고 부스트 압력이 너무 낮습니다.
4. 내부 게이트가 얇고 면적이 너무 작으며 조기에 응고되어 압력 전달 및 액체 금속 공급에 도움이 되지 않습니다.
5. 주조 조직에 핫스팟이 있거나 단면적이 크게 변경됩니다.
6. 용융 금속의 주입량이 너무 적고 나머지 재료가 너무 얇아서 공급 효과를 얻을 수 없습니다.
개선 조치
1. 붓는 온도를 낮추고 수축을 줄입니다.
2. 소형화를 개선하기 위해 사출 비압과 부스트 압력을 높입니다.
3. 내부 게이트를 수정하여 압력 전달을 개선하여 액체 금속 공급 효과에 유리합니다.
4. 주조의 구조를 변경하고 주조의 축적 부분을 제거하고 벽 두께를 가능한 한 균일하게 만듭니다.
5. 두껍고 큰 부품의 냉각 속도를 높입니다.
6. 손잡이를 두껍게 하여 먹이기 효과를 높입니다.
슬래그 구멍
다이캐스팅에는 자체 재료와 다른 금속 및 비금속 입자가 있으며 위치가 고정되어 있지 않습니다. X-ray 검사시 쉽게 발견되지 않으며 가공된 표면에서만 볼 수 있습니다.
원인:
1. 혼합 슬래그:
1) 용융로, 이송 패키지 및 유지로의 라이닝이 떨어집니다.
2) 용해로에서 정련한 후, 용해로를 출고하기 전에 슬래그 제거가 완료되지 않고;
3) 이송 패키지에서 가스 제거 후 표면 찌꺼기가 제거되지 않습니다.
4) 합금액을 유지로에 부을 때 전환 홈이 깨끗하지 않고 여과되지 않습니다.
5) 주입시 홀딩로의 액면에 녹은 슬래그가 제거되지 않고 주입 스푼과 함께 압력실로 유입된다.
2. 흑연 혼합물:
1) 흑연 도가니의 가장자리가 떨어져 합금에 들어갔다.
2) 이형제에 흑연이 너무 많습니다.
개선 조치
1. 캐비티 내부로 슬래그가 최대한 들어가지 않도록 다음과 같은 방법을 사용한다.
1) 퍼니스를 수리하거나 퍼니스 라이닝을 적시에 교체하십시오.
2) 용융로는 공정 요구 사항에 따라 슬래그를 완료하고 적시에 청소해야 합니다.
3) 이송 백의 가스를 제거한 후 표면의 찌꺼기를 청소해야 합니다.
4) 전환 홈이 깨끗한지 확인하려면 전면 끝에 필터 장치를 설치해야 합니다.
5) 유지로의 액체 표면에 스컴을 청소하십시오. 숟가락으로 합금 액체를 떠낼 때 가능한 한 액체 표면에서 떠내십시오.
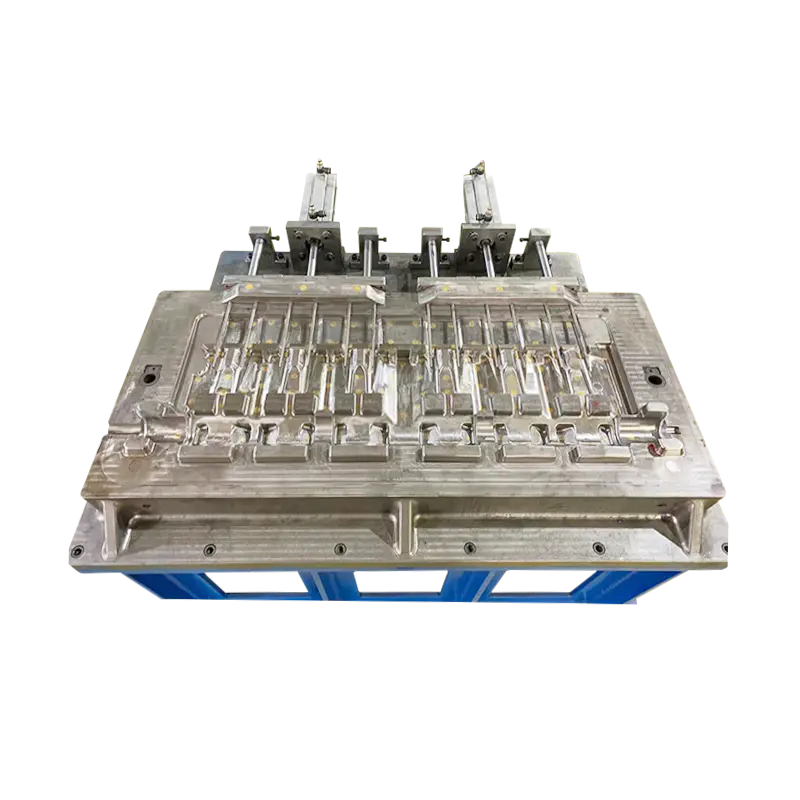