캐비테이션은 캐비테이션이라고도합니다. 움직이는 유체와 가스 사이의 상호 작용으로 인해 유체에 부압(진공 구멍) 기포가 생성되는 경우가 더 일반적입니다. 음압 기포가 이동 또는 유동 과정에서 고체 표면과 만나면 기포가 소멸되면서 거대한 발파 에너지가 방출되어 고체 표면이 오목한 구멍을 형성하게 됩니다. 이 현상은 해수에서 사용되는 블레이드에서 흔히 볼 수 있습니다. 블레이드의 표면은 물과 소용돌이치는 공기의 상호 작용으로 인해 부압 기포를 형성하며, 이는 일반적으로 "포켓"이라고 하는 캐비테이션 피트를 형성하기 위해 블레이드 표면에서 소멸됩니다.
캐비테이션은 알루미늄 합금 고압 다이캐스팅의 생산 공정에서도 발생합니다. 통신 제품과 같은 다이캐스팅 알루미늄 합금 외관 부품 제품의 경우, 때로는 수백 또는 수천 개의 제품을 생산한 후 금형 표면에 오목한 구덩이("포켓"이라고도 함)가 형성되며, 이는 캐비테이션으로 인해 발생하기도 합니다. 이에 따라 알루미늄 합금 부품의 표면에 돌출된 구멍이 생기고 거시적인 모양이 그림 1에 나와 있습니다.
알루미늄 합금 다이캐스팅의 표면에 형성된 "포크 마크"는 "캐비테이션" 외에도 다음과 같은 다른 이유가 있음을 지적해야 합니다. 금형 표면이 EDM 후 완전히 연마되지 않았거나 표면이 금형이 너무 밝으면 이형제가 금형 표면에 우수한 보호막을 형성하지 못하여 금형 표면에 점 모양의 침식 및 금형이 달라 붙습니다. 그러나 금형 표면의 "캐비테이션 침식"에 의해 생성된 피트는 이러한 결함과 모양이 다르며 정확한 판단을 내리기 위해서는 충분한 경험이 필요합니다.
캐비테이션 침식의 원인 알루미늄 합금 다이 캐스팅
알루미늄 합금 다이캐스팅은 액체 알루미늄 합금을 금형의 전체 캐비티에 펀치로 고속으로 주입하여 원하는 제품을 얻는 것입니다. 용융 알루미늄이 흐르는 동안 러너를 통과하여 내부 게이트에 도달한 다음 금형 캐비티에 분사해야 합니다. 금형의 러너는 용융 알루미늄이 흐르는 유일한 경로입니다. 설계원리는 주자의 단면적이 수축상태가 되도록 하여 주자의 공기가 알루미늄용탕의 흐름중에 용탕의 선단으로 배출될 수 있도록 하는 것이다.
캐비테이션이 발생하는 주된 이유는 금형 설계가 위의 설계 원칙을 위반하기 때문입니다. 알루미늄 합금액이 흐르는 러너 경로에서 러너의 단면적이 확장됩니다. 용융 알루미늄이 팽창하는 내부 러너를 통해 흐를 때 체적 팽창과 급격한 압력 강하가 발생하여 용융 알루미늄에 부압(또는 속이 빈) 공동이 형성됩니다. 사출에 압력이 가해지면 캐비티가 러너와 금형 캐비티 내부에서 파열됩니다. 터지면 내부 폭발을 일으켜 막대한 에너지를 생성할 수 있습니다. 제품이 생산될 때 연속적인 다중 내파는 금형 또는 러너 표면에 피로 변형을 일으켜 육안으로 볼 수 있는 구덩이를 형성합니다. 이에 상응하여 주조 제품의 표면에 돌출된 구덩이가 형성됩니다.
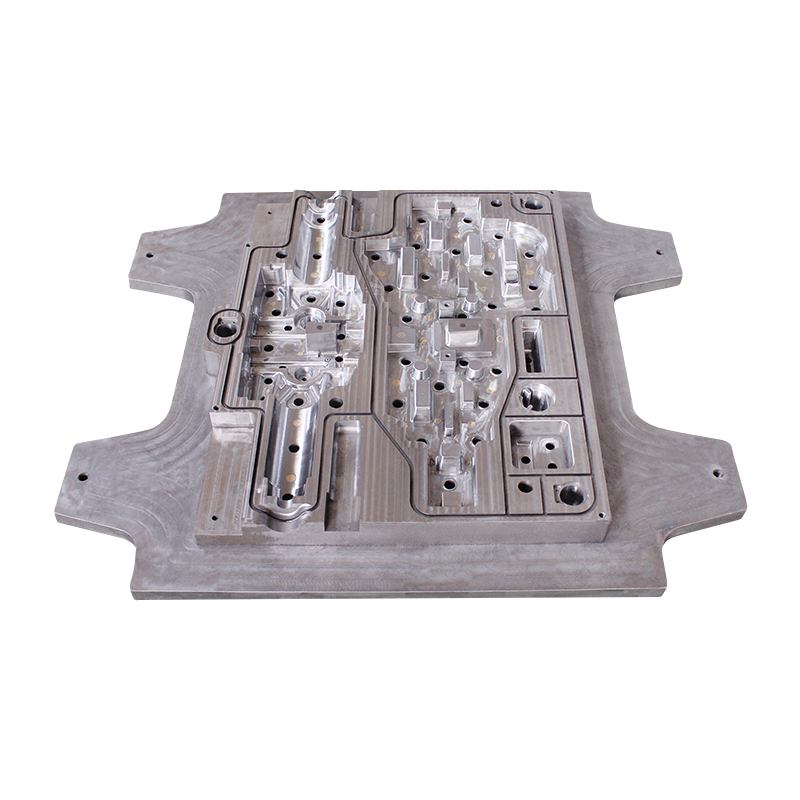